Introduction
DriveWorks allows sheet metal functionality to be controlled
based on your rules. Some sheet metal features are fully
constrained by SOLIDWORKS and do not allow certain parameters to be
captured. This article discusses sheet metal functionality in depth
and suggests alternative methods for controlling the features that
would otherwise be fully constrained by SOLIDWORKS.
Sheet Metal Gauges
The use of a gauge table in the sheet metal part allows the
required gauge to be selected from a drop down list in the
SOLIDWORKS feature manager. As DriveWorks automatically
generates models this is something that needs to be overcome.
Create the gauge table in DriveWorks:
- Locate the gauge table currently in use. This is usually stored
in C:\Program Files\SOLIDWORKS\SOLIDWORKS\lang\
country\Sheet Metal Gauge Tables. When using a
custom table it can be located by editing the sheet metal feature
and clicking the Browse button under Sheet Metal Gauges.
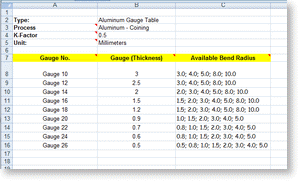
- Open the table in Excel and reformat the data so it can be used
with the
VLookup or
ListAll functions
and includes only the information needed.
Note in the
image below the Available Bend Radius data has been modified so the
original ; separating each available bend radius now uses the |
symbol so it can be used in a list control on the user form. This
column could be omitted altogether if rules can dictate the bend
radius required.
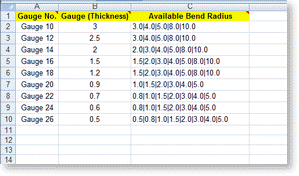
- Open the Project Designer and select Define Tables from the
task explorer. Create a new table and copy the data from the gauge
table into the table in the project designer.
To remove the gauge table from the model and capture the
gauge:
- Open the captured sheet metal part in SOLIDWORKS.
- Locate the Sheet-Metal feature in the SOLIDWORKS feature
manager, right click > edit feature
- Under Sheet Metal Gauges deselect the option "Use gauge table",
click OK to close the Sheet-Metal properties tab
- Double click the Sheet-Metal feature to display the parameters
on the model
- Locate and select the parameter that controls the gauge or
thickness. (This will be shown as a linked dimension.)
- Enter a name for the gauge in the Dimensions and Features
window of the DriveWorks tab.
Bend Allowance/Deduction Table
Bend allowance or bend deduction tables will update the model
when the material gauge or bend radius is changed by DriveWorks. To
actually change the bend table, for instance when the material is
being driven, create the bend table in DriveWorks and drive the
Type and Bend Allowance or Bend Deduction advanced feature
parameter values.
Create the bend table or tables in
DriveWorks:
- Locate the bend table currently in use. This is usually stored
in C:\Program Files\SOLIDWORKS\SOLIDWORKS\lang\
country\Sheetmetal Bend Tables. When using a
custom table it can be located by editing the sheet metal feature
and clicking the Browse button under Bend Allowance.
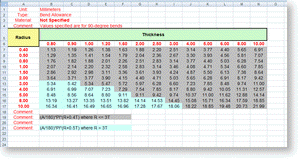
- Open the table in Excel and reformat the data so it can be used
with the
VLookup or
ListAll functions
and includes only the information needed.
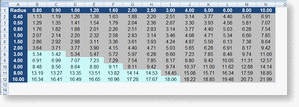
- Open the Project Designer and select Define Tables from the
task explorer. Create a new table and copy the data from the gauge
table into the table in the project designer.
- Follow steps 1 and 2 for any other bend tables that are
required to be utilized.
Remove the bend table from the captured model and capture
advanced feature parameters:
- Open the captured sheet metal part in SOLIDWORKS.
- Locate the Sheet-Metal feature in the SOLIDWORKS feature
manager, right click > edit feature
- Under Bend Allowance select "Bend Allowance" from the drop
down, click OK to close the feature properties tab.
- Select the Sheet-Metal feature from the feature
manager.
- In the DriveWorks Dimensions and features tab enter a name for
the sheet metal feature and click Add to capture the feature.
- Click the "Show Advanced Feature Parameters" link
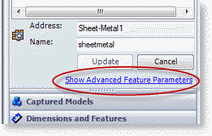
- The advanced feature parameters window can be expanded to show
all available advanced feature parameters for the captured feature.
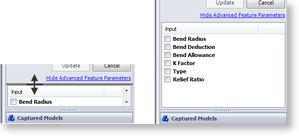
- Select the advanced feature parameters required to be
controlled.
- If the bend allowance type will never change select one from
K Factor,
Bend Allowance or
Bend Deduction
- If the bend allowance type does change select
Type and the required types from
K Factor,
Bend Allowance or
Bend Deduction
- Click Update to update the captured feature with the selected
advanced feature parameters. Click Save on the DriveWorks
toolbar.
Create the rules
When more than one bend table is required create variables that
determine the bend allowance to extract from each, making use of
the
VLookup or .
DWVLookup functions.
Depending on how the bend table is formatted in DriveWorks,
other variables may be required that determine the Radius, Gauge
and column number to use in the Lookup function.
Example
A user form has the option of selecting Steel or Brass for the
material and also a range of gauges for each material.
The variable
DWVariableBendRadius, calculates the bend
radius.
Two bend tables have been added to the define tables section of
the task explorer in the project designer:
- Steel Bend Table
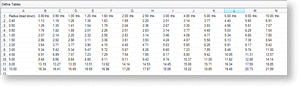
- Brass Bend Table
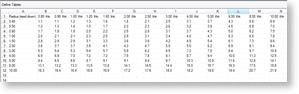
- Create a variable
DWVariableThicknessColumnNumber to determine the
column number to use in the above tables. This could be a series of
nested
If functions
or create another table that lists the available Thicknesses
in one column, with the corresponding column number in another
column, and then make use of the
VLookup function.
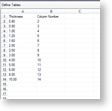
- VLOOKUP(
DWVariableBendRadius,DWLookupThicknessColumnNumber,2,FALSE)
- Create a variable that extracts the Bend Allowance from the
Steel Bend Table (DWVariableSteelBendAllowance) and a variable that
extracts the Bend Allowance from the Brass Bend Table
(DWVariableBrassBendAllowance).
- From the Project Designer select Model Rules from the task
explorer. Select the model the feature has been captured from in
the model list. All captured parameters for that model will be
displayed in the main window, locate the sheetmetal\Bend Allowance
feature parameter, select and click Build.
- Apply a rule for the captured advanced parameter Bend
Allowance to choose which of the two bend allowance variables to
use
- IF(Material = "Steel",
DWVariable
SteelBendAllowance ,
DWVariable
BrasssBendAllowance)
How to drive the Bend Allowance Type
When the bend allowance type has been captured as an advanced
parameter the result of the rule must equal one of the following
values
- BendAllowBendTable
- BendAlllowKFactor
- BendAllowance
- BendDeduction
The bend
allowance type is displayed as
sheetmetal\Type in the Model Rules section.
For example if a BendAllowance was required for a steel
material, and K Factor used for the brass material the rule would
be
IF(Material = "Steel" , "BendAllowance" , "BendAlllowKFactor"
)
K Factor
When sheet metal parts are unfolded using the K Factor to
calculate the developed length, this can be captured and driven
using the advanced feature parameters.
To Capture the K Factor
- Open the captured sheet metal part in SOLIDWORKS.
- Select the Sheet-Metal feature from the feature
manager.
- In the DriveWorks Dimensions and features tab enter a name for
the sheet metal feature and click Add to capture the feature.
- Click the "Show Advanced Feature Parameters" link
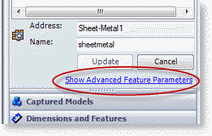
- The advanced feature parameters window can be expanded to show
all available advanced feature parameters for the captured feature.
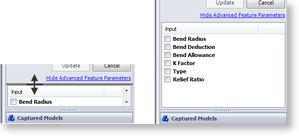
- Select
K Factor from the advanced feature
parameters.
- Click Update to update the captured feature with the selected
advanced feature parameters. Click Save on the DriveWorks
toolbar.
Create a rule for the K factor
- Locate the K Factor parameter for the model in the model rules
section
The K Factor
is displayed as
sheetmetal\K Factor in the Model Rules
section.
- Click Build to open the Rule Builder
- Create a rule that will result in a number to drive into the
captured K Factor
IF(Material = "Steel", 0.5 , 0.4)
Bend Allowance
When sheet metal parts are unfolded using the Bend
Allowance to calculate the developed length, this can be
captured and driven using the advanced feature parameters.
To Capture the Bend Allowance
- Open the captured sheet metal part in SOLIDWORKS.
- Select the Sheet-Metal feature from the feature
manager.
- In the DriveWorks Dimensions and features tab enter a name for
the sheet metal feature and click Add to capture the feature.
- Click the "Show Advanced Feature Parameters" link
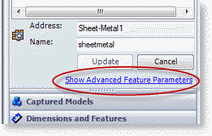
- The advanced feature parameters window can be expanded to show
all available advanced feature parameters for the captured feature.
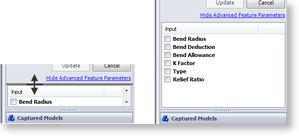
- Select
Bend Allowance from the advanced feature
parameters.
- Click Update to update the captured feature with the selected
advanced feature parameters. Click Save on the DriveWorks
toolbar.
Create a rule for the Bend Allowance
- Locate the Bend Allowance parameter for the model in the model
rules section
The bend
allowance is displayed as
sheetmetal\Bend Allowance in the Model Rules
section.
- Click Build to open the Rule Builder
- Create a rule that will result in a number to drive into the
captured Bend Allowance
IF(Material = "Steel", 0.5 , 0.4)
Bend Deduction
When sheet metal parts are unfolded using the Bend
Deduction to calculate the developed length, this can be captured
and driven using the advanced feature parameters.
To Capture the Bend Deduction
- Open the captured sheet metal part in SOLIDWORKS.
- Select the Sheet-Metal feature from the feature
manager.
- In the DriveWorks Dimensions and features tab enter a name for
the sheet metal feature and click Add to capture the feature.
- Click the "Show Advanced Feature Parameters" link
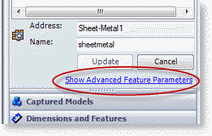
- The advanced feature parameters window can be expanded to show
all available advanced feature parameters for the captured feature.
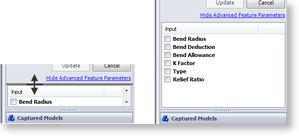
- Select
Bend Deduction from the advanced feature
parameters.
- Click Update to update the captured feature with the selected
advanced feature parameters. Click Save on the DriveWorks
toolbar.
Create a rule for the Bend Deduction
- Locate the Bend Deduction parameter for the model in the model
rules section
The
bend ded is displayed as
sheetmetal\Bend Deduction in the Model Rules
section.
- Click Build to open the Rule Builder
- Create a rule that will result in a number to drive into the
captured K Factor
IF(Material = "Steel", 0.5 , 0.4)
Knowledge Base Article Ref: | KB12121018 |
---|